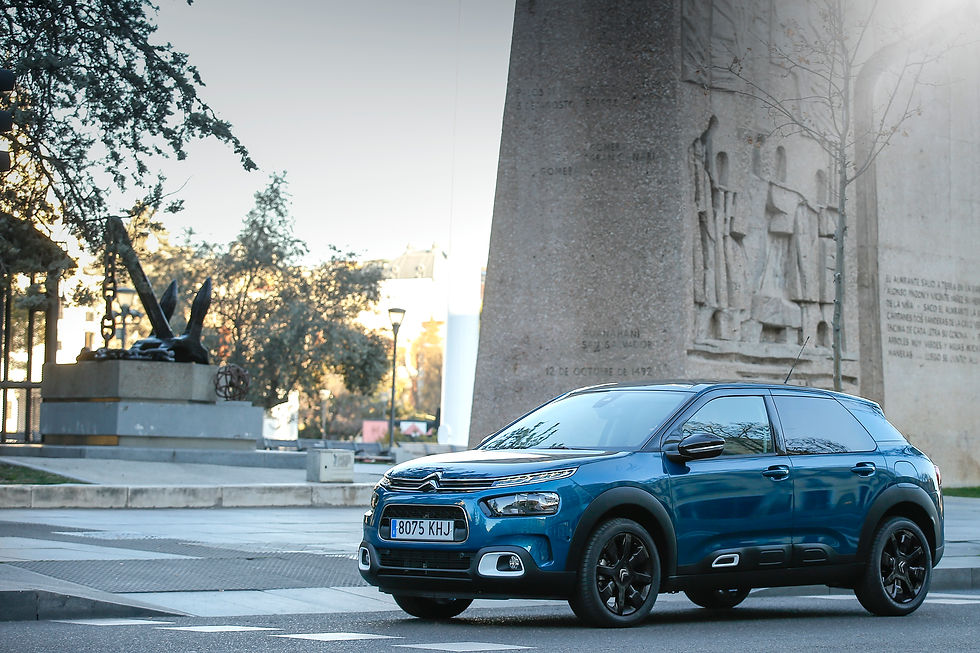
L'usine de Madrid, qui a commencé à transformer les moteurs diesel en 1954, produit en exclusivité la Citroën C4 Cactus dans le monde entier commercialisé dans une cinquantaine de pays
Il faut remonter à 1954 pour parler des origines de l'usine actuelle de Villaverde que le groupe PSA a à Madrid. Après son expérience de transporteur exploitant la ligne de bus Orense-Luintra-Orense, le père d'Eduardo Barreiros fait ses premiers pas dans le monde de l'automatisation. Puis vint le premier atelier familial, dans lequel les moteurs à essence furent transformés en diesel, et qui fut le germe des installations actuelles dans lesquelles est aujourd'hui produite la Citroën C4 Cactus . Il est né en tant que Barreiros Diesel SA, basée à Madrid et avec un capital de dix millions de pesetas de cette époque.
A partir de là, jusqu'à présent, Villaverde a produit des véhicules emblématiques comme la Dodge, la Simca 1000 et 1200, le Chrysler et Talbot 150 amical, la Peugeot 205, Citroen C3 et C3 Pluriel.
L'usine de Villaverde a un avenir prometteur. Il est l' un des trois piliers du groupe PSA en Espagne, avec Vigo et Saragosse grâce à la récompense l'année dernière d'un nouveau projet qui comprend, à l'horizon de 2020/2021, la fabrication d'un nouveau modèle sur une nouvelle plateforme
Un madrilène autour du monde
À l'heure actuelle, le seul modèle produit est la C4 Cactus, dans sa deuxième génération, et est un exemple de la façon dont une ancienne usine a été modernisée, avec un haut degré d'automatisation pour obtenir un nombre de production qui garantissent sa viabilité.
Un temps estimé à 25 heures est nécessaire pour fabriquer chaque nouvelle unité de Citroën C4 Cactus à l'usine de Villaverde. Ce modèle "made in Spain" subit des tests rigoureux de contrôle de qualité, après avoir parcouru près de 5,4 km dans l'usine. Quelque 450 Citroën Cactus partent tous les jours de Madrid .
En plus du personnel qui monte les composants du véhicule à la main, 319 robots sont chargés d'assembler le nouveau Cactus, dont l'automatisation de 96% a été réalisée dans la zone de la tôle où 4096 points de soudure sont appliqués.
Comme une nouveauté pour ce modèle, la carrosserie qui a été précédemment déplacé à travers une ligne d'assemblage est maintenant déplacé par un système magnétique de "chariots autonomes".
L'usine de Madrid, où ce modèle est fabriqué exclusivement pour le monde entier, s'est adaptée aux changements technologiques et aux défis posés par la première génération de ce modèle, lauréate du prix de la meilleure voiture de l'année ABC 2015 , et maintenant de la deuxième génération, dans lequel le confort est la priorité. Dans la ligne d'assemblage, vous pouvez voir, par exemple, des véhicules autoguidés qui suivent la ligne de bandes magnétiques qui transportent les différentes parties de la carrosserie de la voiture aux points de montage. PSA Madrid est la première usine du groupe a avoir ce processus.
Ces lignes magnétiques permettent, par exemple, de faire en quelques heures, un changement effectué dans la chaîne de montage, simplement en faisant varier la course des bandes . Auparavant, il était nécessaire d'intervenir dans toute la chaîne, puisque les pièces parcourues par une chaîne de montage étaient suspendues dans l'air par des rails.
L'utilisation de véhicules autoguidés a considérablement augmenté et le nombre de robots collaboratifs a augmenté dans des tâches telles que le soudage d'éléments métalliques.
Après avoir fait le "squelette" vient le tour de la banque de peinture, avec neuf codes de couleurs différentes. Et une fois la carrosserie mise en forme, nous arrivons à la phase d'assemblage , pour laquelle 1 650 références de pièces sont fournies, dont plus de 800 sont livrées dans des véhicules autoguidés, suivant les mêmes bandes magnétiques qui courent le long du sol. Du tableau de bord aux sièges, en passant par les coussins gonflables et les ceintures de sécurité, le pare-brise, le câblage et, bien sûr, le moteur, ce qui était à l'origine une enveloppe vide prend forme.
La logistique est un autre point très important, car chaque jour, plus d'un million de pièces sont reçues à Villaverde, et chacune d'entre elles doit être au bon endroit à la bonne minute.
Un par un tous les modèles qui sont produits dans l' usine Villaverde passent un circuit de test par des techniciens qualifiés qui font vivre à chaque Cactus produit différents types de chaussées que le conducteur peut trouver en circulation. Dans ce circuit, les spécialistes sont capables de détecter toute défaillance éventuelle de la suspension, dans les réglages des portes, du tableau de bord et du moteur.
«Très récemment, j'ai détecté un son provenant de l'écran multimédia», explique l'un des responsables de la réalisation de ce type de test de qualité. "Au final, il s'est avéré que c'était l'étiquette d'un câble, qui était placé à l'envers, et en passant à travers le pavé il frottait avec un plastique", ajoute-t-il.
Un détail qui, s'il n'était pas détecté à temps, aurait pu causer l'inconfort logique chez le futur propriétaire de la voiture. Mais ce processus de contrôle de qualité n'est pas le seul auquel les véhicules sont soumis, puisque tout au long du processus de fabrication, il est contrôlé que chaque pièce est là où elle doit être.
Depuis 2014, plus de 270 000 unités ont quitté les lignes Villaverde pour la France, du Royaume - Uni, Pays - Bas, l' Italie, l' Australie, le Japon ou l' Afrique du Sud, parmi les cinquante pays où le modèle est exportait .

Villaverde en chiffres:
25 heures approximatives de temps de fabrication.
5,4 kilomètres parcoure la voiture de la tôle à la sortie d'usine
2500 pièces environ compte une voiture
1.000.000 pièces sont reçues quotidiennement à l'usine
90 camions avec neuf voitures partent tous les jours
50 pays comme destination d'exportation
500 gammes de contrôle d'unité dans les véhicules finis
1 500 fonctionnalités révisées
110 km / h de tir de la courbe de puissance
319 robots collaboratifs autonomes dans différents processus
4 096 points de soudure sur le corps
9 codes d'encre avec la nouvelle couleur Emerald Blue

Les véhicules autoguidés transportent les parties du corps vers les points de fixation: hayon, capot et ailes
Dans l'usine de Villaverde, plus d'un million de pièces sont reçues par jour. Chacun d'eux doit être au bon endroit au bon moment, qui commence par assembler les différentes parties du corps, le «squelette» de la voiture.

Dans la section peinture, le véhicule est soumis à une phase préalable qui empêche la corrosion. Le système est automatisé.
Après avoir réalisé tous les assemblages qui composent le corps en tôle, nous passons par le processus de peinture: TTS, cataphorèse, four de dégustation, mastics, scellage, cuisson, finition, laques ...

Des véhicules autonomes autonomes conduisent les véhicules aux différents points où les différents composants sont assemblés
Le véhicule entre dans la zone ASSEMBLAGE, ici, tous les composants du véhicule sont assemblés: Câblage, garniture, planche de bord (tableau de bord), système de freinage, organes mécaniques, sièges, roues, phares, etc.

Au cours de la fabrication et une fois l'assemblage terminé, plus de 1 500 points sont examinés sur la piste d'essai
Une fois ce processus terminé, les voitures finies sont livrées à la ligne de finition, pour son étape ultérieure à la commercialisation
+1 Gros avantage des véhicules filoguidés c’est leu flexibilité par rapport aux convoyeurs aériens.
beau reportage